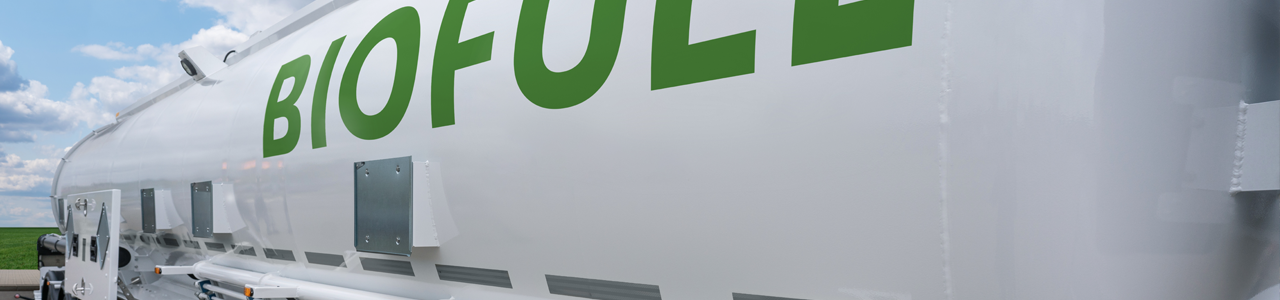
Biodiesel is a first-generation biofuel generated from vegetable oils, including soybeans, rapeseed (canola) and palm. With the ability to reduce lifecycle greenhouse gas (GHG) emissions by as much as 50% compared to fossil-based fuels, biodiesel fits well into the global ambition for clean fuels.
Also known as FAME (fatty acid methyl ester), biodiesel is produced by the process of transesterification using biological feedstock, such as food crops, or latter-generation feedstock such as animal fats, greases and used cooking oil. The benefits of biodiesel are widely ranged. Carbon dioxide emissions from biodiesel are significantly lower, environmental spills aren’t as problematic as pure biodiesel is fully biodegradable, and there is little health risk to humans. Possibly the most impactful aspects of biodiesel, however, is its support of the agricultural industry and contribution to energy security.
Despite its benefits, biodiesel isn’t a perfect renewable fuel. It cannot be used as a drop-in substitute (B100) for fossil-based diesel, and it is limited in concentration (typically up to B20) due to cold climate operations. Higher blends require engine modifications. Demand is primarily seen in North America, Europe, and parts of Asia. It has found usage not only for heavy-duty road transport, but also more recently in marine fuels.
North America, Europe, and Asia continue to invest in biodiesel processing plants. However, this leads to the challenge of finding enough feedstock, especially first-generation virgin plant oil like soy, corn, canola, or palm, to meet the demand for biodiesel. As a result, the utilization of more advanced waste-based and other non-food-based feedstocks of lower carbon intensity should increase. The demand for biodiesel has been increasing. For example, biodiesel production capacity in North America stands at 2.4 billion gallons per year in 2021, with close to 70 plants in operation.
Process
Biodiesel is produced through a process called transesterification, where FAME is formed from the triglyceride (plant or animal oils) by reacting with methanol in the presence of a catalyst. This process causes a separation of two distinct layers—glycerine and crude biodiesel. The glycerine is removed, and the crude biodiesel is then washed and purified, while the alcohol can be recovered and reused.
During this process, just as in the processing of fossil fuels and eventual blending, biofuels must meet a number of specifications, including ASTM D6751 or EN 14214. PAC’s analyzers are the industry standard for monitoring fuel properties. Our analyzers determine FAME content, free and total glycerine, viscosity, cetane number, cloud point, and other properties.
Parameter
|
FAME B100 D6751/EN 14214
|
Bxx D975/EN 590 (to B5) / EN 16734 (to B10), D7467 (B6 to B20) / EN 16709 (to B30)
|
PAC Solution
|
FAME Content |
|
D7371 (FTIR-ATR-PLS)
|
OptiFuel (0-100%)
|
Monoglyceride Content / Free & Total Glycerine |
≤ 0.4% / 0.02% / 0.24% |
|
BioDiesel All-in-One
|
Cetane Number |
≥ 47 |
≥ 40
|
CID 510
|
Viscosity |
@ +40° C |
@ +40° C |
OptiMVD, DFA 70Xi- Cloud Point & Viscosity
|
Cloud Point |
Report |
Report |
DFA 70Xi, OptiCPP
|
Sulfur |
≤ 15 ppm (S15) or 500 ppm (S500) |
≤ 15 ppm (S15) or 500 ppm (S500) |
ElemeNtS
|
Flash Point |
≥ 93° C |
≥ 52°C |
OptiFlash
|
Distillation |
Report |
Report |
OptiDist, OptiPMD
|
A robust FTIR analyzer that combines the capabilities of GS PPA, TD PPA and QuickSpec into one instrument to determine the concentration content of wide varieties of FAME in diesel fuel.
Quickly determines the quality of FAME blending stock for diesel fuel, and yields fast results from a single dedicated system.
A unique technology that is proven to provide the best precision in the market for determining the Derived Cetane Number of all types of diesel fuel, biodiesel, FAME, HVO, BTL, and GTL.
The world’s only instrument that performs four diesel fuel tests in one single unit—cloud point, pour point, viscosity and density, and does it all in less than 25 minutes.
Detects Total Sulfur and/or Total Nitrogen efficiently using ultraviolet fluorescence (UVF) and chemiluminescence (CLD) in diesel fuel and other solid, liquid, gaseous materials or LPG samples.
Accurately detects flashpoint up to 400°C for petroleum products, biodiesels, solvents, chemicals, fluxed bitumen, and food and beverages.
State-of-the-art solution for performing atmospheric distillation, offering the most precision and ease-of-use.
Determines the boiling range characteristics of fuel products in less than 10 minutes, using only 10 ml of sample.
The Fastest and Most Versatile Viscometer and Density Meter
Summary
For countries around the world, biodiesel offers opportunities to comply with environmental regulations, meet long-term carbon reduction goals, and develop a stronger agricultural industry. Life cycle emissions from burning biodiesel are significantly lower—including unburned hydrocarbons, carbon dioxide, carbon monoxide, particulates, and sulfur oxide. With so many benefits, it comes as no surprise that the demand for biodiesel is expected to increase significantly. In response, biodiesel production facilities are being built throughout North America, Europe, and Asia.
As the global leader in advanced analytical instruments, PAC ensures compliance to ASTM D975, D6751, D7467, EN 590 and EN 14214. . Our products deliver highly accurate results, use significantly less sample, and run analysis quickly.
See PAC’s complete portfolio of solutions for diesel: https://www.paclp.com/lab-instruments/application/diesel
Download our brochure on Biodiesel
Please contact PAC for more information and detailed discussion
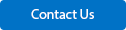